AGL BAYSWATER HEP & SPE/FAC & TAPPING POINT
Client AGL Energy Limited
Location Bayswater Power Station
Job Title HEP & SPE/FAC & TAPPING POINT
Service Planning / Welding / Heat treatment / Scaffolding / Machining / Equipment and tool supply
Scope of Work & Summary of Work Progress
Replacement of main steam drains and “T” section include branch and weld repairs.
Install additional new pressure and temperature tapping points.
Inspection to determine the ongoing fitness for services.
(Summary of Work Progress)
Work Description | Total Progress | Plan | Actual | Variance |
Site Preparation | 100% | 100 | 100 | 0 |
MS -B “T” replacement | 100% | 100 | 100 | 0 |
MS-C “T” replacement | 100% | 100 | 100 | 0 |
HP Bypass “T” replacement | 100% | 100 | 100 | 0 |
LP Bypass “T” replacement | 100% | 100 | 100 | 0 |
MS-B FW07 | 100% | 100 | 100 | 0 |
LB-01 MS | 100% | 100 | 100 | 0 |
LB-01 HPB | 100% | 100 | 100 | 0 |
LB-01 LPB | 100% | 100 | 100 | 0 |
LB-01 HRH | 100% | 100 | 100 | 0 |
Contingency (1 out of 4) | 25% | 20 | 25 | 5 |
Tapping Point | 100% | 100 | 100 | 0 |
SPE/FAC | 100% | 90 | 100 | 10 |
Total | 100% | 89.50 | 91.44 | 1.94 |
`
Project Resourcing
Workshop personnel included Coded Welders and Boilermakers. The support team included Project Management, Quality Management, Project Engineer and Project Supervisor. Protech Welding putted more than 29,000 hours with Zero LTI & MTI for total duration of the work (91days).
Man hrs | Achievement | Duration |
29,736 | ZERO LTI & MTI | 91 Days |
(Health, Safety and Environment Statistics)
No. | Description | Cumulative |
1 | SIF – Serious Impact Fatality | None |
2 | LTI – Lost Time Injury | None |
3 | MTI – Medical Treatment Injury | None |
4 | FAI – First Aid Injury | 1 |
5 | SWA – Stop Work Authority | None |
6 | Near Miss Level 3 | None |
7 | Near Miss Level 2 | None |
8 | Near Miss Level 1 | 2 |
9 | Environmental Incidents | None |
(Health, Safety and Environment Performance (Inc. Subcontractors))
No. | Description | Cumulative |
1 | Safety Interaction | 105 |
2 | Group Take 5’s | 1,396 |
3 | Passive Alcohol Test (Random) | Random |
4 | Supervisor Site Walks | 65 |
5 | Critical Control Check | 6 |
Project Achievements
We’ve proudly completed the project with high standard performance on schedule.
All procedures were qualified and approved by International and Australian standards prior to the project commencement
- Zero (0) Lost Time Incident during the project
- Project delivered on time and under budget
- Protech Welding Pty Ltd worked closely with the client nominated Welding engineer/ consultant in headquarter to ensure all project quality requirements were exceeded for the duration of the project
(Project Weld Achievement)
Description | Total Weld Joints (inc MT / PT / UT) | Total DNC | Weld Failure Rates |
LB-02 – MS B & C Drain Pot T | 15 | – | 0 % |
LB-02 – LP Bypass T | 10 | 1 | 10 % |
LB-02 – MS to HP Bypass T | 4 | – | 0 % |
LB-02 – MS B FW07 Repair | 1 | – | 0 % |
LB-01 – Contingency MS- A | 2 | – | 0 % |
MA-01 – Tapping Point | 27 | – | 0 % |
CMR 235 & Valves – LAD01-01 | 18 | – | 0 % |
CMR 235 – LAC01-03 | 11 | – | 0 % |
CMR 235 – LBC01-03 | 4 | – | 0 % |
Total Weld Achievement | 92 | 1 | 1.08% |
Activities
- Extensive interaction with our client to ensure quality of finished product was in line with practical requirements, especially to set up the repair methodology in the beginning stage.
- Project and quality management
(Safety KPI Activities)
Item No. | Highlights Description |
1 | Dashpivot: Contactless Sign & Out, HSE Management Document |
2 | Pipe Covers & Drop Zone Prevention around Floor Penetrations |
3 | Take 5 Draw (Bunnings Voucher) |
4 | Alcohol Tester in place |
5 | Rigging Tool Box Arrangement & Cabinet |
6 | Permit Board with extra slots for supporting documents |
7 | Drop Prevention installed around work areas (Leather Blankets, plywood, Shade cloth and Uni-mesh) |
8 | Water Station at Level 2 |
Project Images
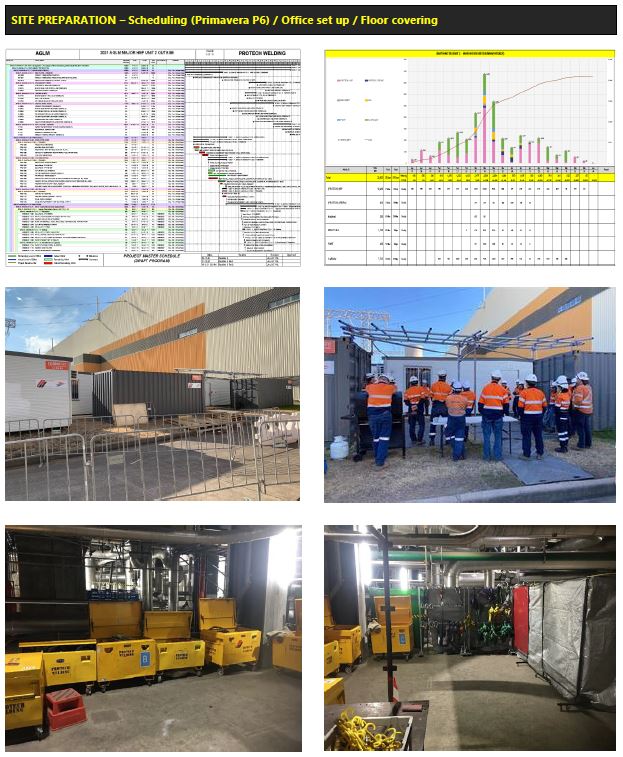
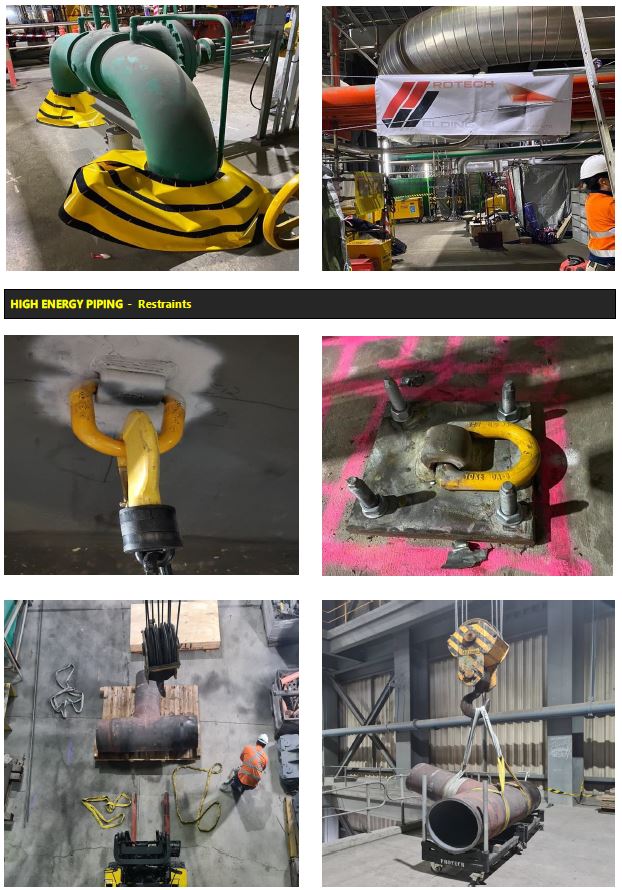
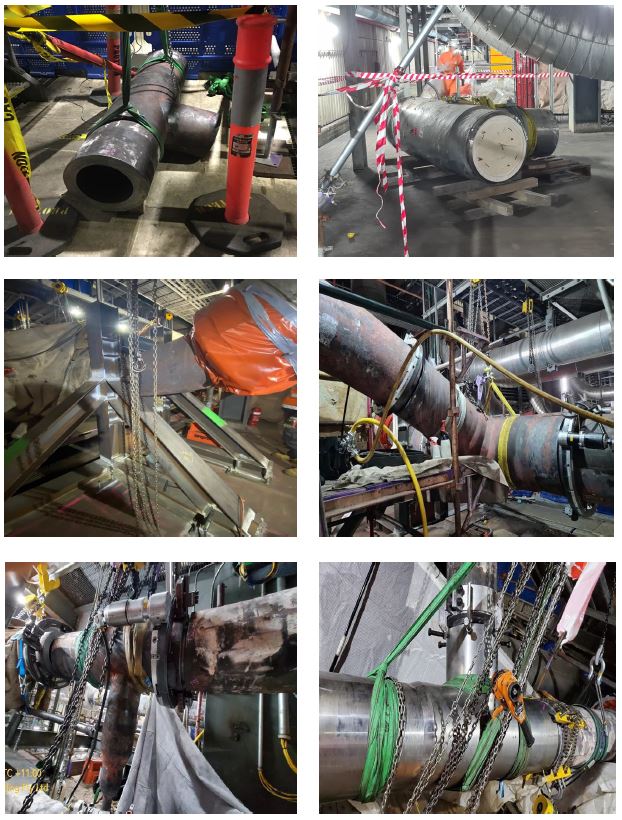
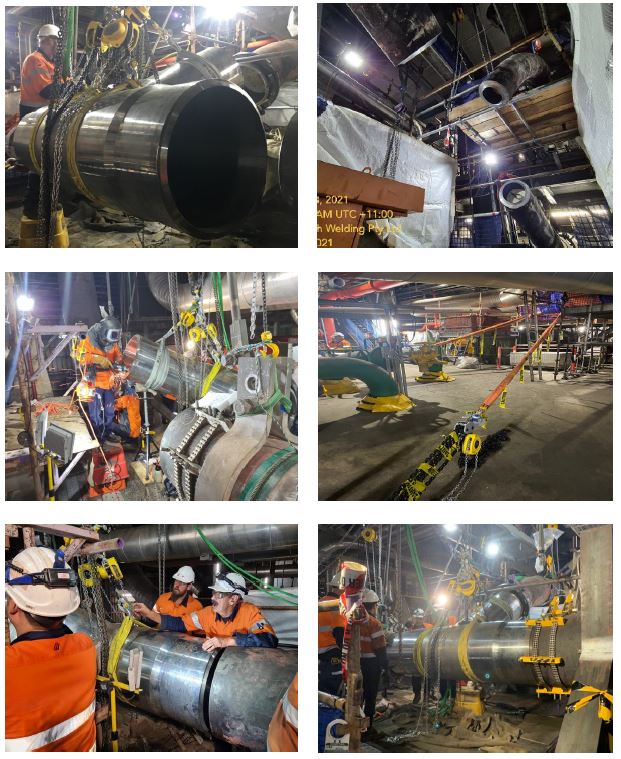
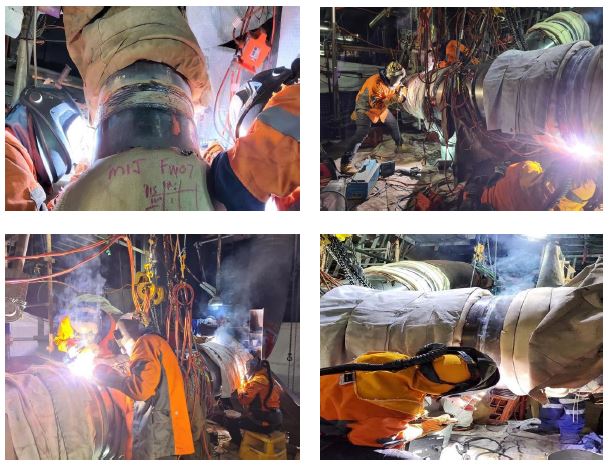
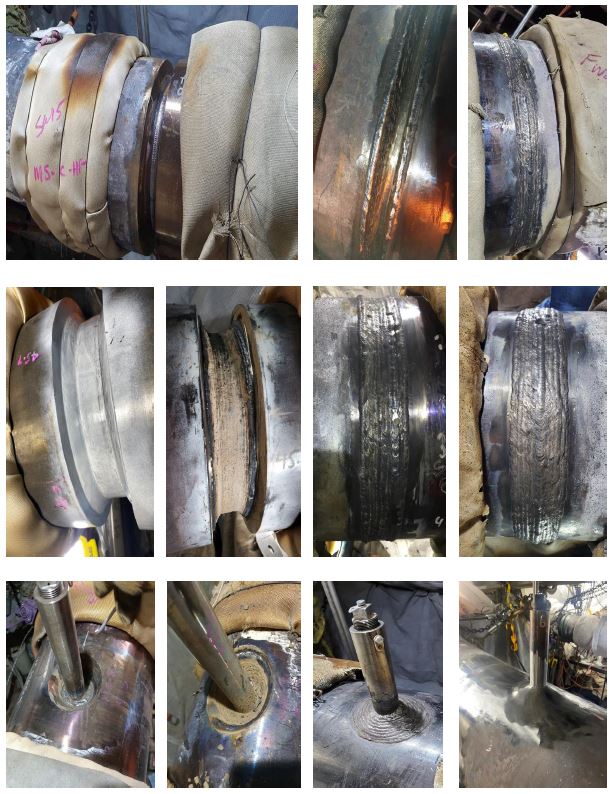
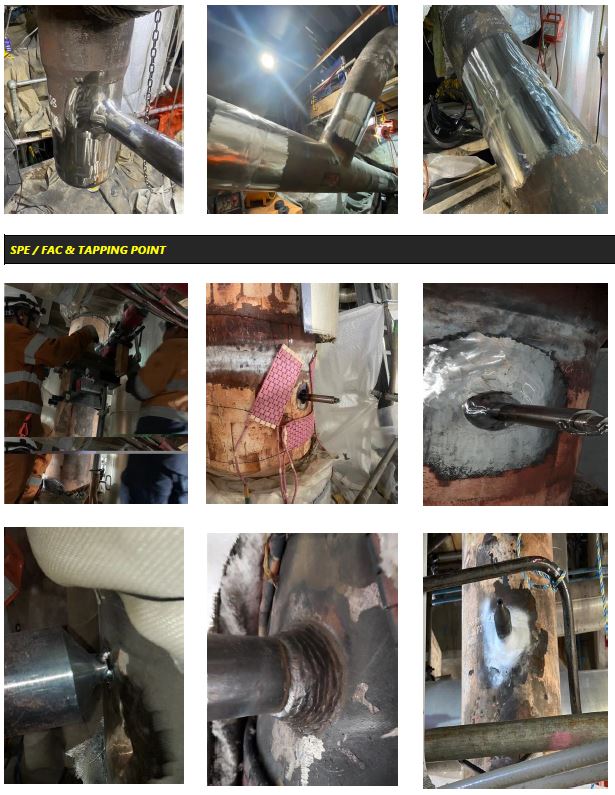
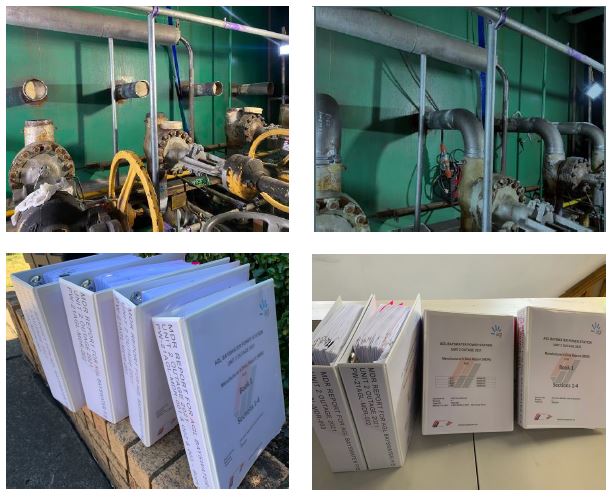